Quick wins to cut industrial energy costs: manufacturers are saving electricity with acoustic imaging
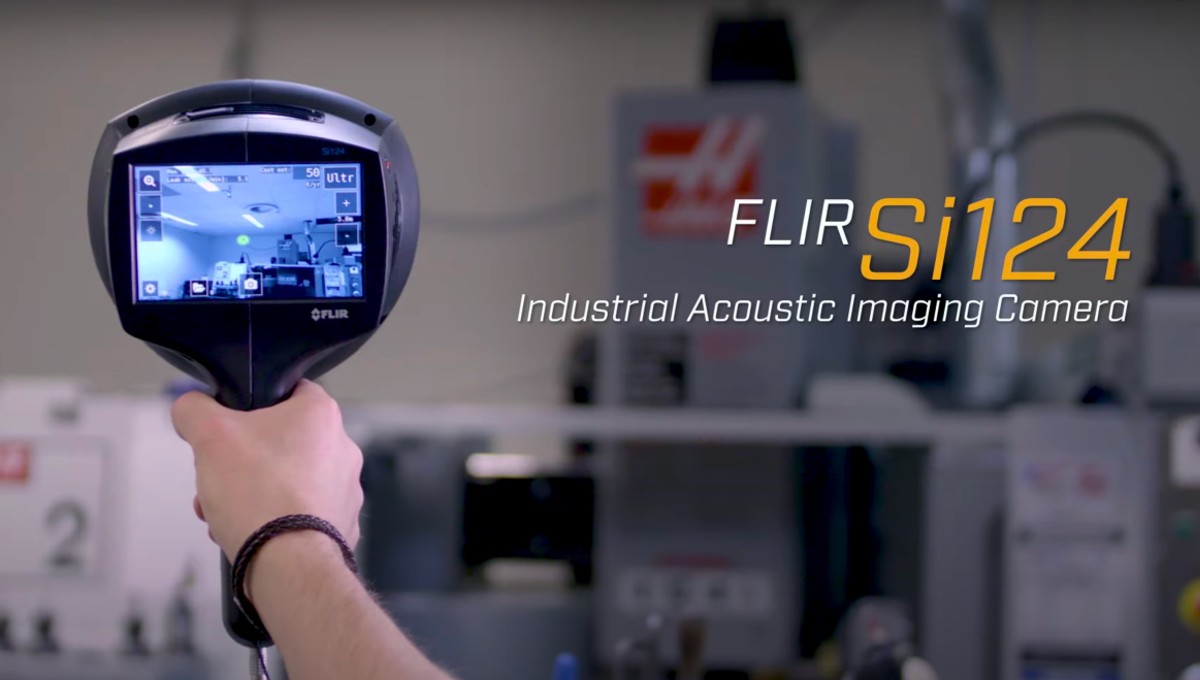
Up to a third of usable energy is lost to compressed air leaks. Stephane Thiebaut, Condition Monitoring Specialist at Teledyne FLIR, explains how to plug holes in your equipment - and your balance sheet
Electricity accounts for up to 75% of all production costs, so it’s no wonder that energy-intensive industries around the world are feeling the pinch right now.
With unparalleled energy prices causing industry expenditure to surge, driving down unnecessary consumption could make the vital difference between production being sustainable or products being written off entirely.
With costs still climbing, manufacturers are under increased pressure to seek out solutions that improve energy efficiency and reduce costs. With no end to the unease in sight, the solution seemingly isn’t either. It exists, of course, but it isn’t in sight; it’s in sound.
Acoustic imaging is cutting operating costs for industrial applications
Energy-intensive industries need a quick win; something that can clearly and measurably demonstrate savings and improve their bottom line. For many manufacturers, acoustic imaging technology is exactly that.
We know that lower energy efficiency means higher energy bills - but how exactly does harnessing sound benefit your balance sheet?
Traditionally, detecting leaks in compressed air systems is especially difficult to locate and, if left unattended, gradually drives up operating costs over time by drastically reducing energy efficiency.
The Teledyne FLIR Si124 acoustic imaging camera detects leaks in compressed air systems up to 10 times quicker than traditional methods - which could equate to saving 10 times the energy lost to maintaining air pressure in an inefficient system.
How costly are leaks in compressed air systems?
You may think that air leaks are a minor concern. But in this case, out of sight is not out of mind - it is simply beyond the detectable range of standard testing. I’ll give you an example: in a typical compressor system, approximately 80% of energy is lost through heat dissipation.
This means that just 20% gets used on the factory floor. From this, up to a third of this usable energy is then lost through further leaks; that’s a loss of up to a third of usable energy - all of which is profit that you can’t see slipping through your fingers.
Acoustic imaging technology such as the FLIR Si124 puts these previously undetectable leaks under the spotlight. 124 microphones combine to cover an optimal bandwidth range of 2 - 65 kHz, which are able to triangulate the location of air leaks by pinpointing even the most minute change in sound.
Truly, this technology offers unmatched detection accuracy - down to even the smallest breach.
An acoustic epiphany: see sound in full colour
The FLIR si124 detects air leaks in industrial environments, regardless of how loud the surroundings are or how minute the breach is.
It shows you the location of a leak in real-time and in easy-to-grasp visuals, by rendering a virtual depiction of the leak on top of a video of the location, so that you can easily identify where the leak is and how severe it is in scope. The intelligent AI embedded within this emergent technology also specifies the severity of the leaks detected, as well as projecting an accurate energy loss calculation over time if not fixed.
This is all vital information that operators can use to evidence the cost of immediate repairs up the line and drive up operational efficiency of their compressed air systems while simultaneously driving down production costs lost to rising energy bills.
In an industry where monetizable assets must be measurable, there is no better tool to have in your arsenal in energy-intensive production environments than the FLIR Si124.
Safer detection of flammable gasses
We’ve exclusively explored compressed air, but other forms of gas in industrial applications also pose a threat not only to production expenses but, much more critically, to life.
The benefit of using an acoustic imaging device such as the FLIR Si124 is that it can detect leaks up to 430 feet away - which could make a vital difference in a setting that could generate an explosion or spark a fire, for example.
As an additional benefit, the technology is incredibly intuitive, meaning that minimal training is required to begin yielding almost instant energy savings across your facility.
Acoustic imaging technology is gaining traction on a global scale - and with such impressive results, it’s clear to see why.
Listen to my recent interview with The Engineer, one of the UK’s leading publications focusing on technological innovation, news and the latest developments in the engineering sector, to learn more about this exciting innovation or delve into the detail of the Si124 range right here.